Concrete Domes for the Storage of De-icing Products
Concrete Dome
Glossary of Terms
1. Shotcrete: A rich concrete mixture
containing 3/8 inch
minus gravel and sand.
Shotcrete is prepared
at a ready mix plant
and delivered to the
job site in mixer trucks.
Shotcrete is discharged
from the truck into a
concrete pump and
sprayed in place over
reinforcement bar.
2. Air-Form: An "air-form" is an
inflatable construction
form. It is made of
fabric similar to roofing
membrane fabric but is
generally much
stronger. This fabric is
cut into gores and heat
welded to make a form
that when inflated will
take the shape of the
finished building. The
air-form becomes an
integral part of the
completed dome. It
stays in place on the
dome. This fabric is
waterproof and
protects the
polyurethane foam.
3. Polyurethane
Foam: Polyurethane foam as
used in the
construction of the
dome is 2lb density
closed cell foam. In
the finished dome it
remains on the outside
of the dome protected
by the air-form. It
provides an efficient
temperature buffer and
an added layer of
waterproofing. |
Insulated reinforced concrete
domes are widely used worldwide to store
a variety of bulk dry products. Domes
built using modern “air-formed”
technology, where construction materials
(shotcrete and reinforcement bar) are
applied on the inside of an inflated airform,
permit a wide range of design
flexibility. The following addresses
design options available to state and
municipal planners as the use of an
insulated all-concrete dome is considered
for the storage of salt and deicing
products.
Insulated concrete domes have
been used to store salt, deicing material
and sand/salt combinations at a number of
locations in the USA. Brown County in
Georgetown, Ohio (2002) uses a dome
that is 100’ in diameter by 50’ in height
for the storage of salt. The Virginia
Department of Transportation (2002)
contains de-icing material in a 140’
diameter by 65’ high dome. The runways
at the Denver International Airport
are maintained by deicing products stored
in insulated concrete domes. Since 1982,
many other states and municipalities have
enjoyed the benefits provided by a
concrete dome for their salt storage needs.
The economic advantages of
insulated reinforced concrete domes
increase as storage requirements (in tons)
likewise increase. The inherent strength
of a concrete dome permits the
containment of a pile throughout the
structure. By contrast domes that use a
concrete cylinder for both product
containment and roof support are
generally limited to storing less than 5000
tons of de-icing material. To understand
how a modern insulated concrete dome is
well suited for salt storage, a brief review
of the construction process is helpful.
Overview of Concrete Dome
Construction
Phase One: Engineering Considerations
The dome must be supported with
a properly designed circular ring beam
footing. The dome shell must also be
properly designed to account for the
external and internal forces carried by the
shell. Consideration is given to how the
de-icing material will enter the dome and
how it will be reclaimed from storage.
Given these and local code considerations,
the engineer designs a dome shell specific
to the project’s requirements.
Phase Two: Site Work, Air-Form
Attachment, and Inflation
The site is excavated, forming is
set, and then concrete is placed around
reinforcement bar within the footing’s
form-work. All construction equipment
and shell re-bar is placed in the center of
the completed footing.
The air-form is attached to the
footing and inflated over the prepositioned
crane and construction
materials. Inflator fans will support the
air-form for the duration of the
construction period.
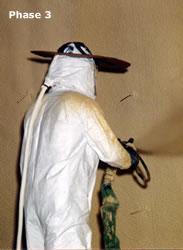
Phase Three: Application of Polyurethane
Foam
Polyurethane foam is sprayed to
the underside of the inflated air-form.
Embedded in the
foam are thousands
of wire insulation
hangers or “stickers”. These
stickers will provide
anchor points that
will hold the re-bar
steel in place
throughout the dome.
Because the foam is
first placed inside the
inflated air-form,
when the dome is
completed, the foam
will actually be
outside the shell and
under the air-form.
Phase Four: Placement of Re-bar and
Shotcrete
Inside the inflated air-form, Grade
60 reinforcement bar is placed according
to design requirements. Shotcrete is then
applied in thin layers in a method that
ensures proper coverage of the rebar steel.
Quality assurance standards must
be rigidly enforced along with ongoing
safety procedures. A customer should
insist on review of the contractor’s safety
and quality assurance program and require
credentials that demonstrate successful
construction of similar projects. Once the
shotcrete is applied and the reinforcement
bar is properly embedded to the design
depth, the major construction effort is
complete. The shell is now ready for the
finish work.
Conclusion
The modern insulated, reinforced
concrete dome offers superior strength and
wide design flexibility. Because the dome
shell is insulated on the outside,
exterior temperature swings don’t
as readily produced interior
moisture. The dome’s strength
allows for loader operation without
fear that the structure will sustain
damage. The shell is virtually
fireproof and leak-proof. It can
handle extremely high winds and
seismic forces. Dome Technology
maintains a web site to aid
engineers and potential customers
as the use of a dome is considered.
Due diligence in proper pre-design
analysis is important to ensure that
the most efficient shape and size of
dome is specified for the
requirements of the project.
Other Design
Considerations
If available
property is limited,
then perhaps a dome
incorporating a stemwall
is most suitable
for consideration.
If product is to be
reclaimed by frontend
loader or by an
offset under-ground
discharge system,
the dome can be
designed to facilitate
an "asymmetrical"
pile. In this design,
product is loaded just
off the dome's apex,
rather than directly
through the center
top of the dome.
Due to the
inherent strength of
concrete domes,
large openings for
conveyors or for
other purposes can
be incorporated into
the shell design.
Likewise, tunnels (if
required) for outbound
product, can
be constructed either
above or below
grade.
Jeff Crandall
Senior Sales Rep.
Dome Technology, Inc.
Idaho Falls, ID
www.dometech.com |